4 Easy Facts About Alcast Company Shown
4 Easy Facts About Alcast Company Shown
Blog Article
Our Alcast Company Ideas
Table of ContentsAbout Alcast CompanyFacts About Alcast Company UncoveredAlcast Company Can Be Fun For EveryoneThe Facts About Alcast Company RevealedAlcast Company Things To Know Before You Buy9 Easy Facts About Alcast Company Described
Chemical Comparison of Cast Aluminum Alloys Silicon advertises castability by lowering the alloy's melting temperature level and boosting fluidness during casting. Additionally, silicon contributes to the alloy's strength and put on resistance, making it beneficial in applications where durability is essential, such as automobile parts and engine components.It likewise enhances the machinability of the alloy, making it much easier to process into completed items. In this way, iron contributes to the overall workability of light weight aluminum alloys. Copper raises electric conductivity, making it useful in electrical applications. It likewise boosts rust resistance and contributes to the alloy's overall toughness.
Manganese adds to the strength of light weight aluminum alloys and boosts workability (aluminum casting company). It is typically used in functioned aluminum items like sheets, extrusions, and profiles. The visibility of manganese aids in the alloy's formability and resistance to cracking during fabrication procedures. Magnesium is a lightweight element that gives stamina and effect resistance to aluminum alloys.
Alcast Company for Dummies
It enables the manufacturing of lightweight elements with superb mechanical buildings. Zinc enhances the castability of aluminum alloys and helps control the solidification process throughout spreading. It boosts the alloy's toughness and hardness. It is frequently discovered in applications where detailed forms and great information are necessary, such as decorative castings and specific auto components.

The primary thermal conductivity, tensile strength, yield strength, and elongation vary. Amongst the above alloys, A356 has the highest possible thermal conductivity, and A380 and ADC12 have the lowest.
Not known Facts About Alcast Company
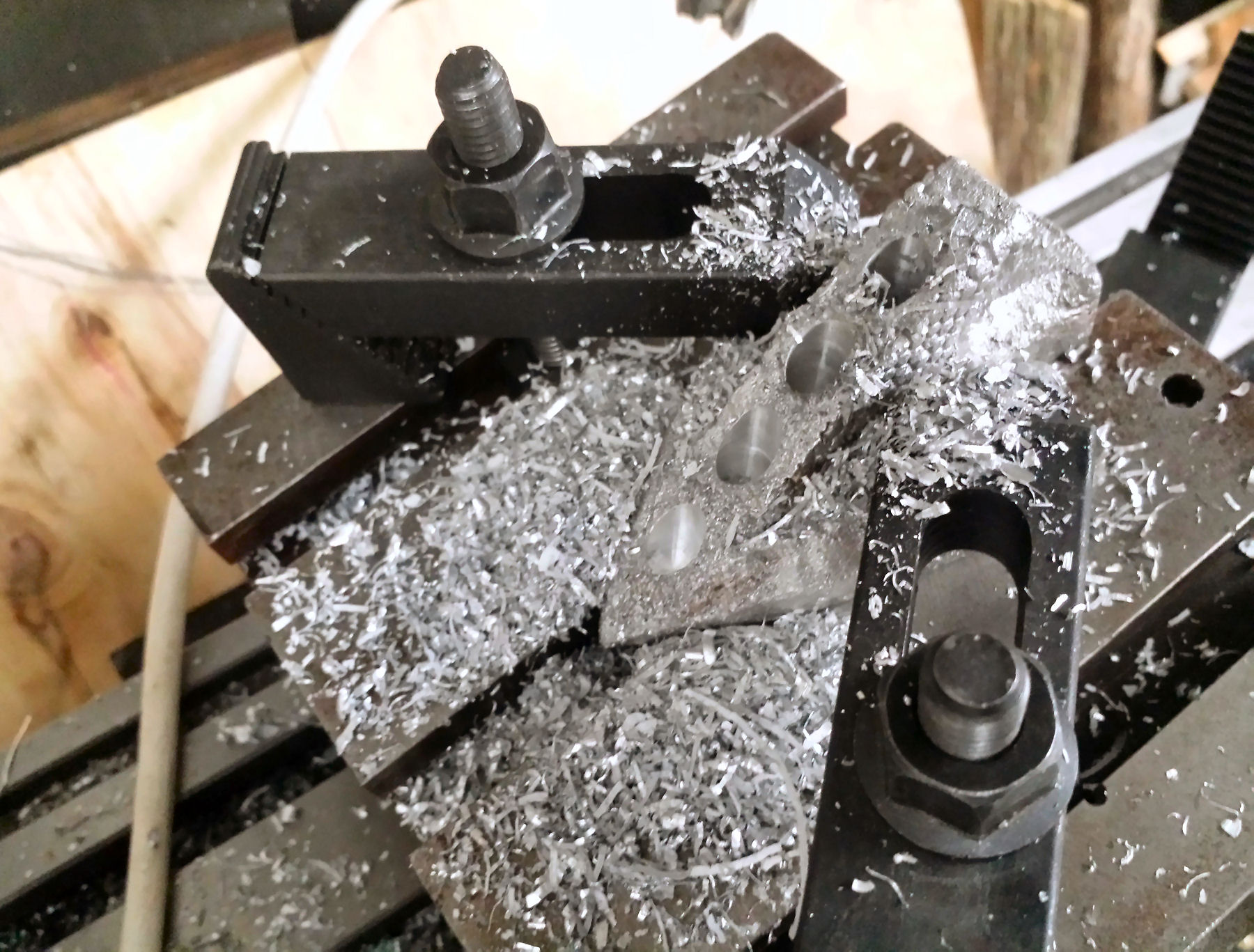
In accuracy spreading, 6063 is well-suited for applications where complex geometries and top notch surface finishes are extremely important. Examples consist of telecommunication units, where the alloy's exceptional formability permits sleek and visually pleasing layouts while maintaining structural stability. In the Lighting Solutions industry, precision-cast 6063 components produce sophisticated and effective lights components that call for detailed shapes and good thermal performance.
It brings about a better surface finish and much better deterioration resistance in A360. Furthermore, the A360 displays remarkable elongation, making it suitable internet for complicated and thin-walled parts. In precision casting applications, A360 is fit for markets such as Consumer Electronics, Telecommunication, and Power Tools. Its improved fluidity enables complex, high-precision elements like mobile phone cases and interaction gadget real estates.
About Alcast Company
Its unique homes make A360 a beneficial selection for precision casting in these industries, enhancing product sturdiness and high quality. Foundry. Aluminum alloy 380, or A380, is a widely used casting alloy with several distinctive attributes.
In accuracy casting, aluminum 413 beams in the Customer Electronic Devices and Power Tools markets. It's generally utilized to craft complex components like smartphone real estates, cam bodies, and power tool housings. Its accuracy is amazing, with limited resistances approximately 0.01 mm, ensuring remarkable item assembly. This alloy's exceptional corrosion resistance makes it an outstanding choice for outdoor applications, making certain durable, long lasting items in the discussed industries.
The 10-Second Trick For Alcast Company
When you have actually determined that the light weight aluminum die casting procedure appropriates for your project, an important following action is determining on the most ideal alloy. The aluminum alloy you choose will significantly affect both the spreading process and the buildings of the final item. Due to this, you need to make your choice meticulously and take an informed method.
Establishing the most ideal light weight aluminum alloy for your application will certainly suggest considering a wide selection of features. The very first classification addresses alloy features that impact the production procedure.
Some Known Details About Alcast Company
The alloy you select for die spreading straight affects a number of aspects of the spreading process, like how very easy the alloy is to collaborate with and if it is vulnerable to casting flaws. Warm splitting, additionally called solidification splitting, is a common die casting flaw for light weight aluminum alloys that can result in interior or surface-level rips or cracks.
Certain aluminum alloys are much more prone to warm fracturing than others, and your option should consider this. It can damage both the cast and the die, so you must look for alloys with high anti-soldering buildings.
Corrosion resistance, which is already a significant feature of aluminum, can vary considerably from alloy to alloy and is a necessary particular to consider depending on the environmental conditions your product will be exposed to (Aluminum Casting). Wear resistance is an additional home frequently sought in aluminum products and can distinguish some alloys
Report this page